Esbelt All-in-one Compact Air-cooled Presses
For vulcanizing conveyor belts. Now available in widths of 600mm and 1200mm. More widths coming soon.
Control panel, compressor and cooling system integrated into the chassis of the presses.
Main benefits:
Excellent for on-site vulcanizing.
Especially handy where water source is not easily available (eg. in sugar refineries, flour mills or new installations where water supply is not available yet).
Exceptional versatility for a wide range of thicknesses.
The gradual heating system ensures the complete fusion of the internal layers as well as the outer covers. Thus ensuring a strong belt joint. With a nominal distance of 20mm between top & bottom plate, these presses are perfect for belts of all thicknesses or embossed belts requiring the silicone molds.
Strong belt joint.
The thorough fusion of the belt ends through all belt layers makes the belt joint area nearly as strong as the rest of the belt.
Flat and even joint.
The robust structure of the press chassis guarantees a uniform pressure along the entire width of the press. Even if the belt is much narrower than the press, the belt joint remains flat and even.
For thin belts, work as well even without film.
The uniform pressure along the press keeps the joint area of thin belts flat even without using film.
Successive joints without modifying parameters.
Various joints of the same belt type can be carried out consecutively without having to change the initial splicing parameters while maintaining the quality of the splices.
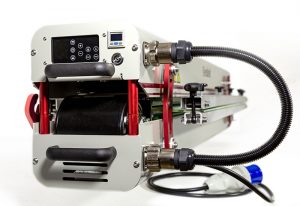
Simple connections: top & bottom plate and electrical supply.

Integrated control system.
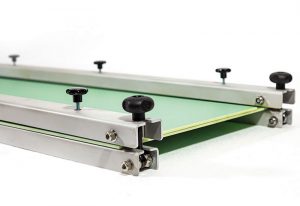
Stratified fibreglass plates for more even temperature distribution.

In-built wheels at one end of the press facilitate press mobility.
Optional travelling box sold separately.